Other Failure Cases
Bomber Crash into Empire State Building
On July 28, 1945, a ten-ton (10,000 kg) B-25 bomber crashed into the Empire State Building at an estimated 400 kph, into the north face of the 79th floor. Although several people were killed, the building remained standing (Levy and Salvadori, 1992).
To estimate the force applied to the building, we must estimate either the deceleration of the bomber as it crashed into the building (and use the force-acceleration method), estimate the distance it took the bomber to come to rest (and use work-energy), or estimate the time it took to bomber to come to rest (and use impulse-momentum). The bomber did not pass through the building, so a distance of 10 to 20 meters for the plane to come to rest could be used for calculations. If the bomber came to rest in 20 meters with a constant deceleration, the force would be about 4440 kilonewtons exerted over about 0.25 seconds.
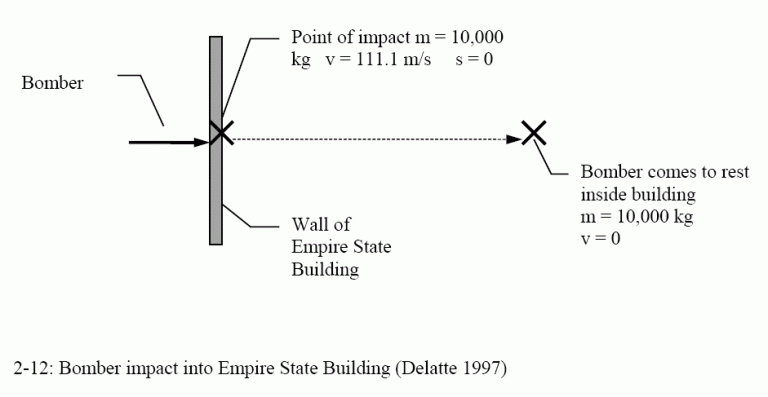
All three of these methods are derived from F = ma. The acceleration is assumed to be constant and is integrated once for velocity and twice for distance traveled. This problem is useful for demonstrating the equivalence of the three methods.
This case study was originally written in 1997 (Delatte, 1997), well before the terrorist attacks of September 11, 2001 (see World Trade Center and Pentagon). The same methods may be applied to calculated the impact forces applied by any aircraft of known weight and speed, with an estimate of the average distance before the aircraft (or its parts) came to rest.
Reference: Levy and Salvadori, 1992.
Comet Jet Aircraft Crashes
One of the first commercial jet aircraft was the British de Havilland Comet, which first flew in 1952. By 1954, seven of the Comets had crashed under unknown circumstances. Since only 21 had been built, the one-third failure rate was catastrophic. The impact of the Comet crashes was the loss of Britains early leadership in commercial passenger jet aircraft.
One plane crashed about a half hour after takeoff from Rome, with the wreckage falling into the sea between the islands of Elba and Monte Cristo. The Tyrrhenian Sea was shallow enough for the British Royal Navy to recover the wreckage.
While the investigation was continuing, fifty structural modifications were made to the Comets. They were cleared to fly again, but within two weeks another crashed.
Researchers assembled and examined the wreckage. A large number of theories including sabotage and pilot error were considered and discarded. The hypothesis that best fit the circumstances was metal fatigue.
The Comet had square windows, like an earlier unpressurized propeller-driven passenger planes. The square windows had severe stress concentrations at the corners, which increased stresses and reduced fatigue life. Examination of the wreckage showed cracks initiating at the corners of the windows and propagating into the plane’s fuselage. Stress concentrations and fatigue loads, as at the Point Pleasant Bridge, make a deadly combination. Today, aircraft windows are round or oval, without sharp corners.
The solutions are fatigue resistant design, coupled with an extensive program of inspection and maintenance. Bridges, aircraft, and other structures subjected to fatigue are designed to eliminate stress concentrations as much as possible. Smooth transitions are used where lines of stress change direction. Connections and details prone to fatigue are identified, and maintenance schedules are followed to inspect or replace these components periodically.
See Chapter 3 of the book Beyond Failure: Forensic Case Studies for Civil Engineers, Delatte, Norbert J., ASCE Press 2009.
The Comet crashes are covered in one chapter of Levy and Salvadori (1992, pp. 121-126). In addition, a chapter of Freiman and Schlager (1995, pp. 78-86) covers the incidents. This case study is also featured on the History Channel Modern Marvels Engineering Disasters 4 videotape/DVD.
Liberty Ship Fatigue Failures
The Liberty Ships of World War II were an engineering and industrial solution to a specific military and political problem. The problem was that is was necessary to build merchant ships faster than the German Navy submarines could sink them, in order to supply the United Kingdom and sustain its war effort. The problem was complicated by the fact that the Great Depression had greatly reduced U.S. shipbuilding capacity.
Between 1930 and 1937, U.S. shipyards built only 71 merchant ships. However, 5,777 were built between 1939 and 1945. This was made possible by changes to construction methods, as well as the standardized Liberty freighter and similar T2 tanker designs. One shipyard built a Liberty ship in five days. The massive increase in production was possible in large part because of a change from riveted to electric-arc welded construction. Shipyards were organized for maximum efficiency around the welding process. New welding equipment was developed for heavy steel ship plate. The German pocket battleships had pointed out the efficiencies of welded ship hulls. By saving a thousand tons of weight in the hull, they could carry that much more armament (Tassava 2003, pp. 90-93).
One of the best known Liberty Ship failures was the S.S. Schenectady.
At 10:30 pm on January 16, 1943, an explosive boom shattered the cold night that had settled over the Swan Island shipyard outside Portland, Oregon. Rushing to the fitting-out docks where the yards T2 tanker vessels were completed, graveyard shift workers discovered that the yards very first ship, the S.S. Schenectady, had cracked in half amidships. The ships deck and side shells had fractured completely; only the plates running along the bottom of the [162 m] 532-foot long hull held the fore and aft sections together. (Tassava 2003, p. 87).
Although this wasn’t the first cargo ship failure, it was highly visible, as the first ship built in the new yard. In March, another tanker, the Esso Manhattan, split in half while entering New York harbor. In January 1943, about 20 ship failures occurred, with 4 or 5 suffering Class I damage or total hull failure like the Schenectady . Twenty Class I failures occurred in January 1944, with 120 failures in the following March. Many failures occurred in the open ocean. Since the Schenectady and Esso Manhattan failures occurred in port, the ships could be put in drydock, repaired, and put back into service (Tassava 2003, pp. 88 -90).
The solutions fell into three categories improvements to shipyard practice, retrofits of the completed ships, and changes to the design. Two different anti-fracture design changes were made. The first was to redraw the Liberty ship plans to round off the troublesome hatch corners. The second was to install crack-arresting devices, to stop cracks from propagating through the hulls. It had been observed that fractures were generally stopped by perpendicular barriers such as riveted or especially strong seams (Tassava 2003, p. 101). In the early Class I failures, such as the Schenectady and Esso Manhattan, the cracks had been able to travel completely through the hull.
The gunwale bars and the other retrofits were successful. No ship with gunwale bars ever failed in service. Through the end of the war, only 127 of the 4,694 Liberty ships and T2 tankers ever suffered a Class I fracture, and no ships with anti-fracture devices failed. Two years after the war an official board of investigation determined that faulty workmanship caused exactly 25 % of the 2,504 fractures which had occurred up to August 1, 1945, that a combination of inferior workmanship and inadequate design caused another 20 %, and design so poor that perfect workmanship would have done little to prevent the failures caused a stunning 55 % (Tassava 2003, p. 103).
The complete case study is provided in Chapter 9 of Beyond Failure: Forensic Case Studies for Civil Engineers. A useful review of the Liberty Ships, as well as the problems and solutions of welding, was written by Christopher James Tassava, Weak Seams: Controversy over Welding Theory and Practice in American Shipyards, 1938 1946, History, and Technology, Vol. 19 No. 2, pp. 87-108 (Tassava 2003). Tassava is a historian, not an engineer, but does a good job of reviewing the technical issues associated with the failures. This case study is featured on the History Channel Modern Marvels More Engineering Disasters videotape/DVD. However, the History Channel version seems oversimplified.
Space Shuttle Challenger
The Challenger exploded 73 seconds after launch on January 28, 1986. It was the 25th shuttle mission. The seven astronauts killed included a high school teacher, Christa McAuliffe, who was to broadcast lessons from space. Government investigations and redesign efforts grounded the shuttle program for the next two years (Freiman and Schlager 1995a, p. 161).
The Challenger explosion was investigated by a presidential commission, as well as the U.S. Senate and House of Representatives. This disaster represented a rare engineering failure where a number of people knew the cause immediately.
The Rogers Commission, appointed by President Ronald Reagan, recorded 15,000 pages of testimony and reviewed 170,000 pages of documents and hundreds of photographs. More than 6,000 people were interviewed as part of the three-month investigation. The commission’s findings were released on June 6, 1986, in a 256-page report. The House Committee on Science and Technology also conducted hearings and issued a report. After the incident, a number of astronauts and other key personnel resigned from NASA (Freiman and Schlager 1995a, pp. 169-171).
The U.S. House of Representatives Committee on Science and Technology report (Committee on Science and Technology 1986), “Investigation of the Challenger Accident, October 29, 1986,” is available on-line at http://history.nasa.gov/rogersrep/51lcover.htm and http://www.gpoaccess.gov/challenger/64_420.pdf. A summary is provided in Freiman and Schlager (1995a, pp. 161-172). Two ethics websites, http://onlineethics.org (Case Western Reserve University 2007b) and Texas A&M University (http://ethics.tamu.edu/ethics/shuttle/shuttle1.htm Space Shuttle Challenger Disaster 2007), feature this case study.
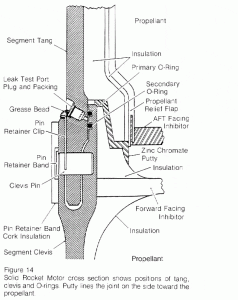
Transcona Grain Elevator
The Transcona Grain Elevator collapsed in 1913, and the Fargo Grain Elevator collapsed in 1955, with almost identical failure mechanisms. They were similar structures founded on similar types of soil. The two cases provided important confirmations of soil bearing capacity calculations.
Transcona Grain Elevator
Construction of the elevator started in 1911. It consisted of a work house and a bin house. The work house was 21 by 29 m (70 by 96 ft) in the plan, and 55 m (180 ft) high, with a raft foundation 3.7 m (12 ft) below the surface. The bin house had 13 bins, each approximately 28 m (92 ft) high and 4.3 m (14 ft) in diameter. The bins rested on a reinforced concrete raft foundation, 23.5 m (77 ft) wide and 59.5 m (195 ft) long, also at a depth 3.7 m (12 ft) below the surrounding soil. The underlying soil was a layer of stiff blue clay, roughly 6 to 11 m (20 to 35 ft) thick (Peck and Bryant 1953).
Small plate load tests were performed before construction. These indicated that the soil should be able to bear a pressure of 383 to 479 kPa (4 to 5 tsf or ton per square foot). The total pressure with the warehouse filled with grain would be no more than 316 kPa (3.3 tsf) (Morley 1996, p. 26).
The structure was finished in September 1913 and began to be filled with grain as uniformly as possible. On October 18, 1913, the bins were about 88 % full, and the settlement was observed, increasing within an hour to a uniform 300 mm (1 ft). Over the next 24 hours, the structure tilted to the west by nearly 27. Surprisingly, the bin house remained intact through the rotation (Peck and Bryant 1953).
The development of soil mechanics after the Transcona failure eventually provided a basis for computing the ultimate bearing capacity of soils. It was subsequently realized, therefore, that the Transcona failure served as a full-scale check of the validity of such computations. (Shepherd and Frost 1995, p. 5).
Fargo Grain Elevator
The Fargo Grain Elevator collapsed 42 years after the Transcona Grain Elevator. Major filling began in April 1955, and the collapse occurred on June 12, 1955. The structure broke apart and was completely destroyed in the collapse. It collapsed in the northward direction, forming a mass of concrete rubble and grain with soil heaved up on the south side as much as 1.8 m (6 ft). Like the Transcona Grain Elevator, the Fargo structure was part of the ancient Lake Aggassiz clay deposits that stretch across much of the northern Great Plains of North America (Nordlund and Deere, 1970). Figure 7-7 shows the elevation and plan of the failed grain elevator.
The Fargo Grain Elevator was a reinforced concrete structure comprising 20 circular bins and 26 small interstitial bins. The circular bins, arranged in two rows of 10 bins each, were 5.8 m (19 ft) in diameter and 37 m (122 ft) high. The foundation was a reinforced concrete raft 16 m (52 ft) wide, 66 m (218 ft) long, and 0.7 m (2 ft 4 in) thick. It was thus narrower but longer than the Transcona Grain Elevator, with about 75 % of the capacity. The edge of the foundation was thickened, and the bottom of the raft was 1.8 m (6 ft) below grade excluding the thickened edges. Steel sheet piling was also driven around the edges of the foundation (Nordlund and Deere, 1970).
Settlement readings were taken on the raft foundation starting on May 10, 1955, a month before the collapse. Seven elevation benchmarks were established, and readings were taken once per week. There was no record of any possible settlement before the benchmarks were established. Settlements increased dramatically over the week and a half before the collapse, reaching 222- 308 mm (8.75-12.13 in). It is clear that a day-to-day plot of these data would have given clear warning of the impending failure (Nordlund and Deere, 1970, p. 589).
References
The complete case studies are provided in Chapter 7 of Beyond Failure: Forensic Case Studies for Civil Engineers. The two-grain elevator failures occurred 42 years apart, and the landmark papers analyzing the failures were written nearly two decades apart. In each case, the authors went into great detail concerning their field sampling and laboratory testing procedures, as well as the methods they developed to estimate the shear strength of the soils. Readers interested in those details should obtain and read the original references.
The key references on these cases are by Peck and Bryant (1953) on the Transcona Elevator and by Nordlund and Deere (1970) on the Fargo Elevator. Morley (1996) discusses the significance of Transcona and other cases in the development of geotechnical and foundation engineering as a discipline.
Peck, R.B., and Bryant, F.G. (1953) The Bearing-Capacity Failure of the Transcona Elevator, Geotechnique, Vol. 3, pp. 201- 208.
Nordlund, R.L, and Deere, D.U. (1971) The collapse of the Fargo Grain Elevator, ASCE Journal of the Soil Mechanics and Foundations Division, Vol. 96, No. SM2, pp. 585-607, March 1970.
Illustrations from Chapter 7 of the book Beyond Failure: Forensic Case Studies for Civil Engineers, Delatte, Norbert J., ASCE Press.
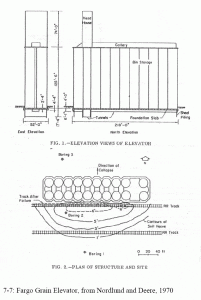
Willow Island Cooling Tower
Twenty-eight-day cylinder strength tells you how strong a concrete cylinder cured in a laboratory is at 28 days. It doesn’t necessarily tell you much about how strong the concrete in the structure is. The strength gain of concrete is highly dependent on ambient temperature. In cold weather, the concrete in a structure will be much weaker than laboratory cylinder strength would predict.
The Willow Island, West Virginia cooling tower collapsed while under construction on April 27, 1978, killed 51 workers in the worst construction disaster in U. S. history (Lew et al. 1979, Ross 1984, Kaminetzky 1991, Feld and Carper 1997). A jump form system was being used, with the forms secured by bolts in one-day and three-day-old concrete. The forms were designed to be progressively moved up the tower as it was built. The temperature had been in the mid-thirties at night. The National Bureau of Standards found that the concrete had not attained enough strength to support the forms. The report concluded that the most probable cause of the collapse was the imposition of construction loads on the shell before the concrete of lift 28 had gained adequate strength to support these loads (Lew et al. 1979).
References:
- Feld, J., and Carper, K. (1997). Construction Failure. 2nd Ed., John Wiley & Sons, New York, N. Y.
- Kaminetzky, D. (1991). Design and Construction Failures: Lessons from Forensic Investigations.
- McGraw-Hill, New York, N. Y.
Ross, S. (1984), Construction Disasters: Design Failures, Causes, and Prevention. McGraw-Hill, New York, N. Y. - Lew, H., Fattel, S., Shaver, J., Reinhold, T. and Hunt, B. (1979). Investigation of Construction Failure of Reinforced Concrete Cooling Tower at Willow Island, W.V., U.S. Department of Labor, OSHA/National Bureau of Standards, Washington, D.C.
Illustrations from Chapter 9 of the book Beyond Failure: Forensic Case Studies for Civil Engineers, Delatte, Norbert J., ASCE Press.
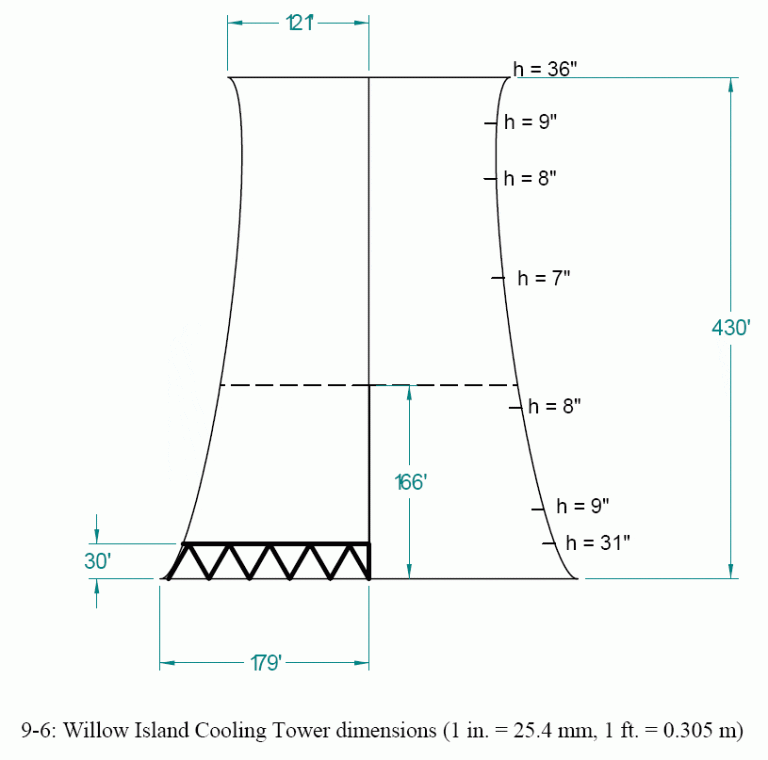
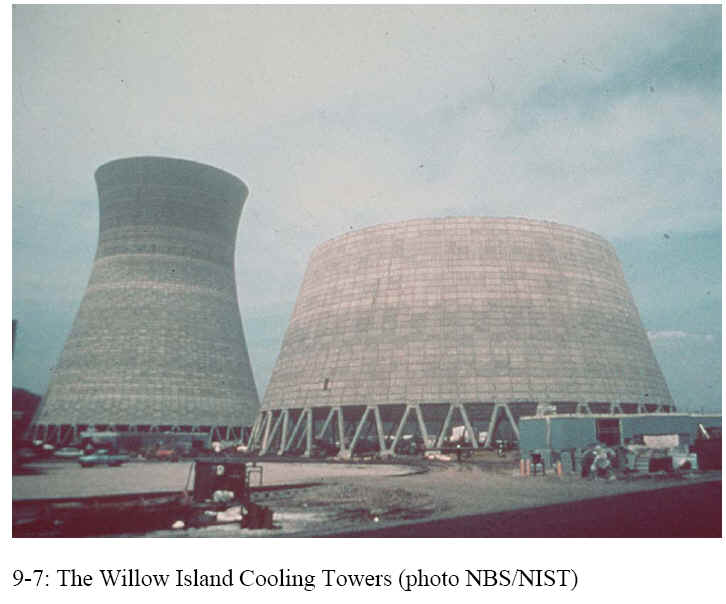
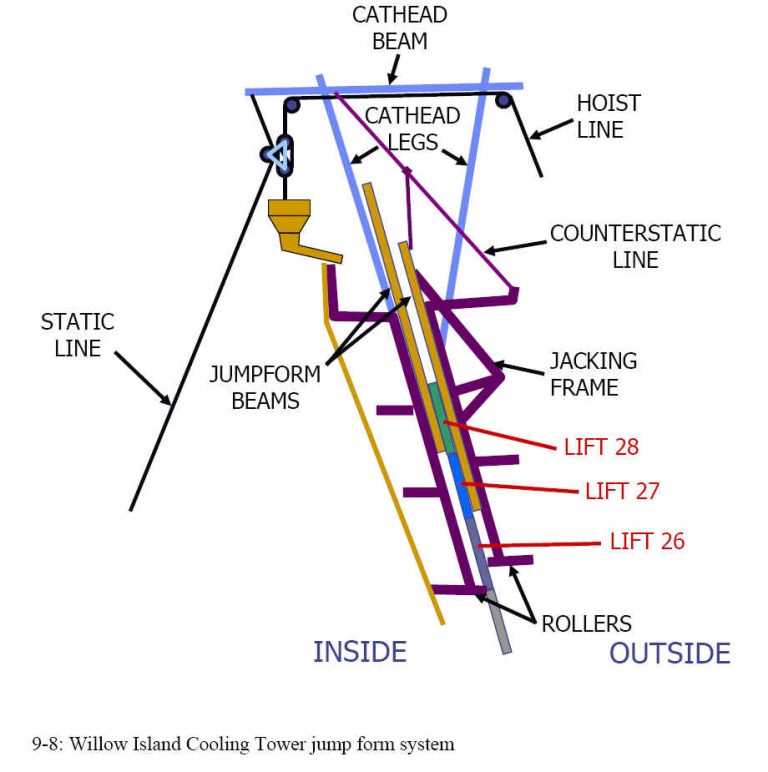
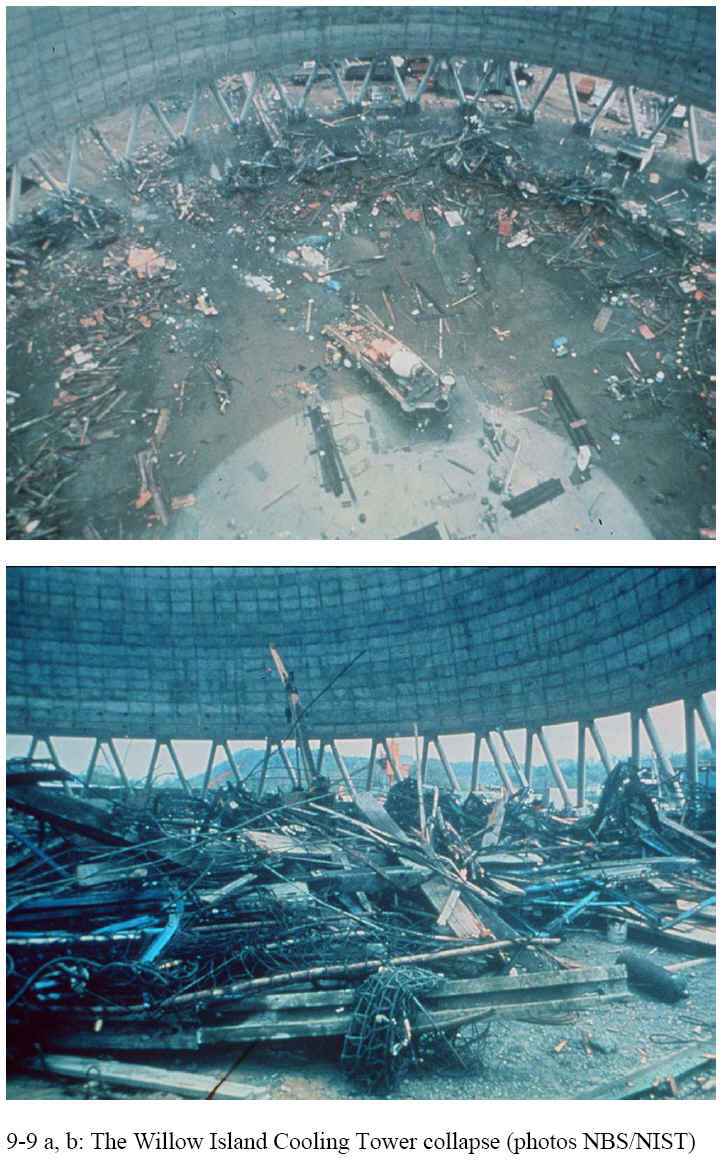