International corporation Oerlikon Additive Manufacturing contributes equipment to W.S. Lee College of Engineering
Equipment donation expands research capabilities in advanced manufacturing
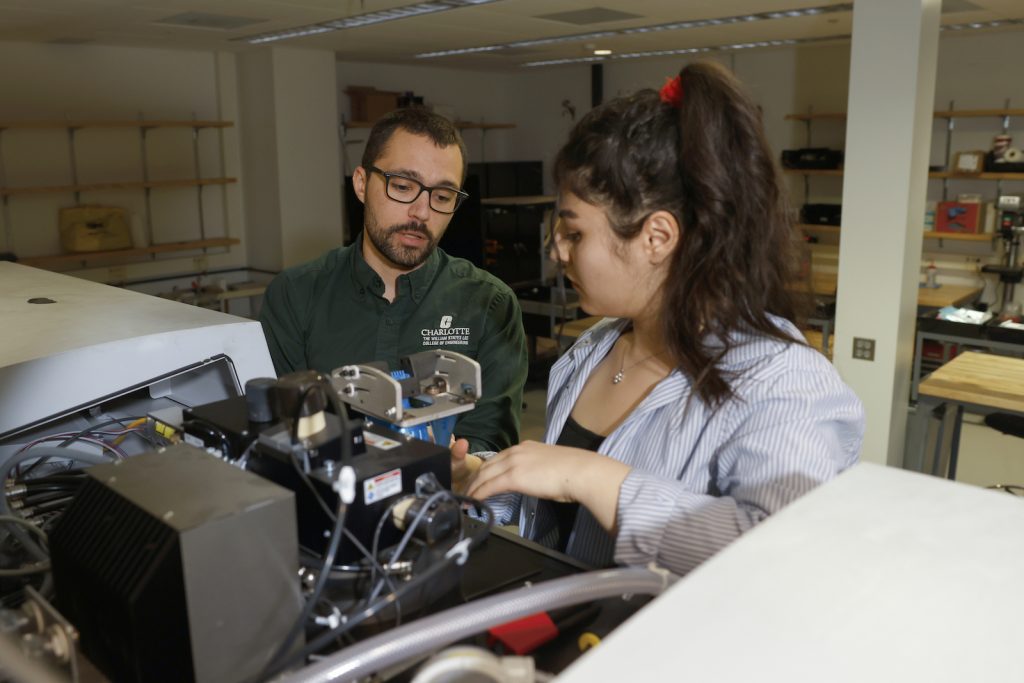
This academic year, one of the world’s leaders in metal additive manufacturing, Oerlikon AM donated an industry-grade metal additive manufacturing machine to William States Lee College of Engineering’s Department of Mechanical Engineering and Engineering Science, demonstrating its continued commitment to research and discovery.
With this donation, the company and college both position themselves to continue increasing their leadership in the expanding AM industry. Luke Dee, Oerlikon AM’s Process Engineering Manager at the company’s U.S. headquarters explains why the company turns to the nationally ranked engineering college for a partnership. “We recognize the critical role of additive manufacturing in American industry,” said Dee. “UNC Charlotte’s engineering college will be a pivotal research resource as we continue to lead the technology forward.”
About the equipment
Almost the size of a minivan, the donated equipment, an M280 laser powder bed fusion system made by Germany’s EOS GmbH, is a commercial-grade 3D printer that uses powdered metal feedstock rather than filament like most tabletop 3D printers. Laser powder bed fusion systems of this type are used to manufacture components for industries such as aerospace, automotive, power generation and more, where strength, precision and durability are required.
Jaime Berez, assistant professor of mechanical engineering, understands these requirements on a deeper, more technical scale due to his research expertise in additive manufacturing. He directly manages the M280 and is incorporating it as a key tool in his research.
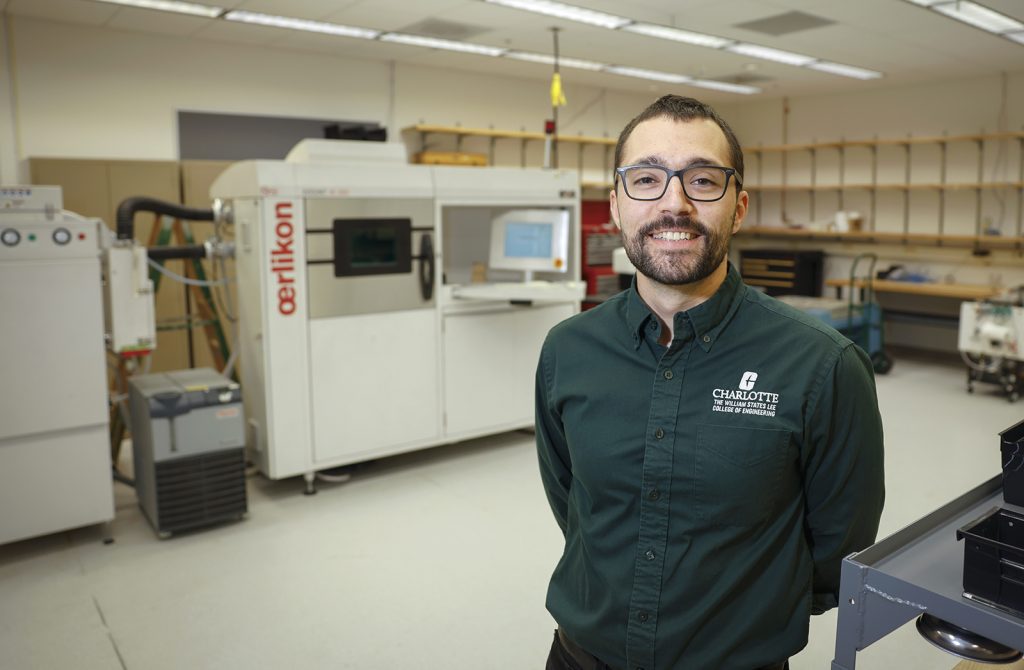
“This manufacturing equipment allows us to conduct research that is relevant to the current needs of industry,” said Berez. “These machines can process alloys that can withstand the high-temperature combustion environment of a jet engine, as well as alloys that can remain chemically inert and safe for biomedical devices. The M280 allows me and other faculty to research in a new realm using advanced materials that are used in current production processes.”
The M280 is designed to be a powerful tool for industry, producing large batches of parts for commercial use. But it also provides delicate precision for intricate detail work, which makes it extremely sensitive to its surroundings. It requires a very controlled environment for user safety and part quality. The W.S. Lee College of Engineering was able to provide exactly that – a specialized lab space for the equipment with a controlled environment that monitors humidity and limits vibrations. In these labs, engineering faculty and graduate students will be trained by professionals on machine usage and maintenance, ensuring a quality process and safety.
The power of additive manufacturing
To better appreciate metal AM, one must compare it to traditional manufacturing methods, such as casting and forging which require long lead-times and specialized tooling. Likewise, machining requires removing material from a larger piece of metal and creating waste in the process. In these traditional processes, smaller components may have to be individually manufactured and assembled to arrive at the finished part.
However, metal AM technology offers an increasingly important technology for industry, enabling novel highly complex component designs while reducing waste and decreasing lead-time. Users have the ability to build the entire part (or a consolidation of many parts) using only the material needed. It combines components at the printing stage, rather than during construction. Fine geometries intended to optimize performance can also be produced, allowing for more design complexity and improved product performance.
The potential for impact
The expansive potential behind AM is leading industry to explore new ways to provide solutions in the future, and engineers are leading that exploration.
“I’m currently researching the health monitoring and performance testing of these AM machines, trying to understand how they succeed and fail when pushed to their limits,” said Berez. “The goal is more repeatable and trustworthy equipment and processes when producing components such as the turbine blades in gas turbine power generators. Charlotte’s a good place to be right now. It’s supporting not just my research, but the future of additive manufacturing overall.”
Oerlikon AM US, Inc., the American headquarters of the Swiss corporation, is based in Huntersville, North Carolina. The company provides metal additive manufacturing solutions that create lighter weight, more durable parts; optimize parts production by minimizing material waste, improving quality and creating more reliable components. By offering additive manufacturing metal powders, additive component manufacturing, and advanced surface treatments, including PVD, CVD, and thermal spray coatings, Oerlikon is uniquely positioned to advance the industrialization of additive manufacturing.