Fulbright Fellow Collaborating with UNC Charlotte to Produce Concrete from Waste Materials
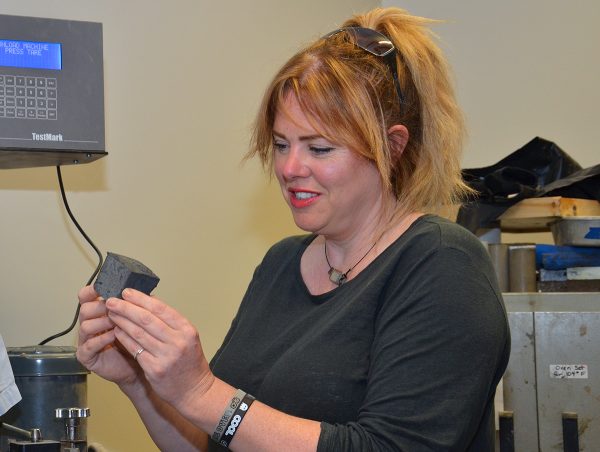
For her Fulbright Fellowship research, Irish Ph.D. student Roisin Hyde wanted to expand her studies of incorporating waste materials into the manufacturing of concrete. Her goal brought her to UNC Charlotte to collaborate with Civil Engineering Associate Professor Dr. Brett Tempest, who is known for his pioneering research in the development of coal fly ash concrete.
A student at Queen’s University Belfast, Hyde was a practicing architect in Ireland for 15 years before returning to school to pursue her doctorate. She won a Fulbright Visiting Researcher grant in the summer of 2018 to expand her research in the development of a high-performance, low-impact, cement-free geopolymer concrete façade panel.
“I had been working in Ireland using locally generated industrial by-product and waste materials, such as blast furnace slag and quarry dust,” Hyde said. “I read about the geopolymer concrete façade panels Brett produced for the 2013 Solar Decathlon. He was the first person to successfully create geopolymer concrete sandwich panels made from coal ash. The project was groundbreaking as a full-scale application using an alternative cement made using chemically-activated waste material.”
Concrete is one of the world’s most common building materials, and is traditionally produced by mixing Portland cement with aggregate materials such as sand and rock. Portland cement is produced by firing limestone, a process that yields more than 0.75 tons of CO2 emissions for every ton of cement produced. The clinker production and energy consumed by the kilns in the manufacture of Portland cement are responsible for about 6 to 8 percent of the world’s carbon emissions.
Geopolymer cements are formed by chemically activating materials in a strong alkaline solution. The resulting paste can be mixed with aggregates and cured to form high-performance concrete. Geopolymer concrete is a low-carbon alternative to Ordinary Portland Cement, and they can be made using industrial by-product and waste materials such as coal ash furnace slag, incinerator ash and recycled materials.
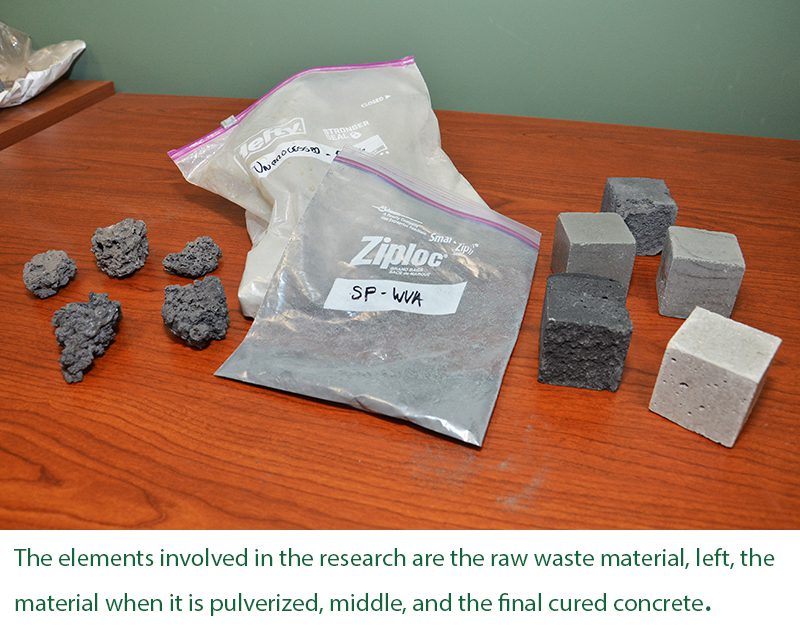
“Our geopolymer concrete research at UNC Charlotte has been almost exclusively with coal fly ash,” Dr. Tempest said. “When Roisin called and said she was interested in working with us to explore the use of other alternative waste materials, we were thrilled. Being able to branch out into other waste materials has been very helpful. Roisin has is extremely resourceful working with area companies and getting materials to experiment with.”
The companies and the waste materials they are providing currently include Gerdau, smelter waste from steel recycling; Martin Marietta Mallard Creek Quarry, ultra-fine granite dust; West Virginia Alloys, silica fume; Sunrock Quarries, basalt quarry dust; and Lehigh-Hanson, granulated blast furnace slag. For use in geopolymer concrete, researchers crush the material to sizes ranging from one micron to 3 millimeters, before chemically-activating it with an alkaline solution.
“We are fortunate that modern digital analytic technologies and chemistry allow us to identify suitable materials through x-ray diffraction and others methods to see how well they will work in concrete,” Hyde said. “For centuries construction workers have just been using trial and error to see what worked. Now we can analyze nano-properties and adapt our mixes. This takes a lot of the guess work out. It is quantifiable.”
In addition to developing ways of making geopolymer cement, Hyde is also researching more environmentally friendly methods for forming the material into concrete. As an architect, Hyde works with thin high-performance concrete used for cladding building exteriors with complex geometries. The creation of such concrete panels currently produces large amounts of waste.
“There are a lot of opportunities for eliminating waste in the way high-performance concrete is manufactured,” Hyde said. “Current techniques use custom-made polystyrene molds. The concrete is poured into flexible rubber molds which are placed on the polystyrene form, covered and then vacuum-sealed to remove air bubbles. Once cured, all of the molding material and packaging is thrown away.”
Hyde is developing a re-configurable system where the concrete is placed in the mold, vibrated and then shaped by an array of digitally adjustable pins.
“I want to know, what can you make with this material and how will it fit into the design of an actual building,” Hyde said? “I think I’m very application based, which is why I’m fitting in well at UNC Charlotte.”
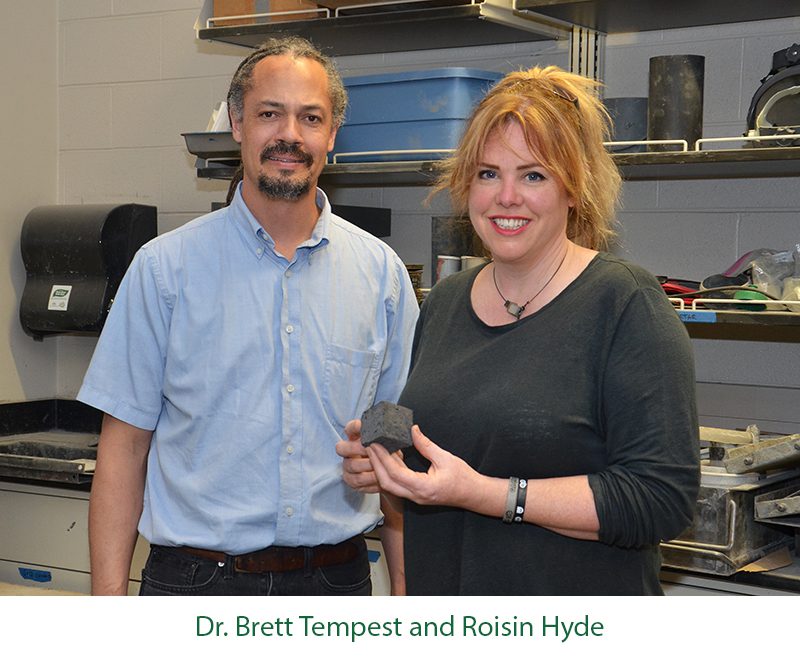
The draw of UNC Charlotte for Hyde was the combination of its culture and facilities. “A lot of things about UNC Charlotte are very special,” she said. “The facilities are amazing and the labs are incredibly well equipped. There is also a hands-on attitude here that you don’t see at a lot of other institutions. You get your hands dirty here.”
Overall, working with industry representatives and fellow researchers in the United States has been a great experience, Hyde said. “People in the U.S. have been very welcoming and supportive. There is a positivity and optimism here. There is also wonderful teamwork and collaboration.”
In addition to working with Dr. Tempest at UNC Charlotte, Hyde is also collaborating with Dr. John Daniels and undergraduate research assistant Samantha Tonog from Civil Engineering; Dr. Rachel Dickey and Alex Cabral from Architecture; and Dr. Deborah Thomas, Dr. John Diemer and Jonathan Watkins from Geography and Earth Science.
Additional information about Hyde’s research is available online, including:
A comedy culb talk that uses red cabbage to demonstrate environmental impact.
An article in Silicon Republic about producing construction materials that are kinder to the environment.