Nishant Ojal to Start LLNL Post-Doc Position
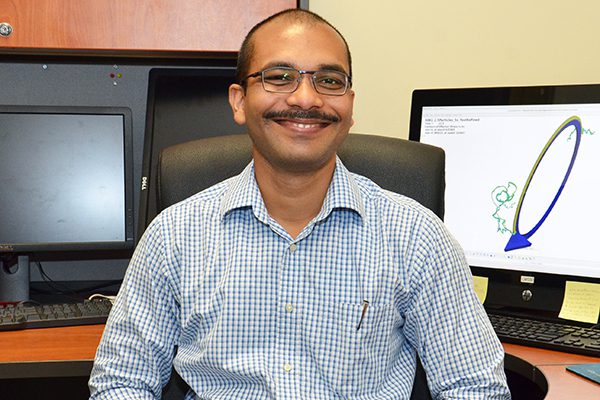
Mechanical Engineering Ph.D. student Nishant Ojal will be going to Lawrence Livermore National Laboratory after he graduates this summer, continuing work he started during an internship with LLNL last semester, which involved researching ways to improve additive manufacturing.
Ojal will be defending his doctoral thesis at UNC Charlotte on July 6th. His thesis work has been on computational analysis of the manufacturing methods involved in machining. Because of an interest in metrology, he also completed the graduate certification in precision metrology. He also worked in a round-robin project of the Center for Freeform Optics (CeFO) as a lead student. The project is about the intercomparison of different metrological instruments used for measuring freeform optics.
“My work at UNC Charlotte has been the modeling of machining processes,” Ojal said. “Besides having experience in computational analysis, I have been fortunate to learn actual machining on conventional and CNC machines from an inspirational teacher, Brian Dutterer”.
Ojal’s faculty mentor for his thesis is Dr. Harish Cherukuri, who in addition to computational machining work has also had a long relationship with LLNL, researching new methods for additive manufacturing (also known as 3D printing).
“The work Nishant is doing in modeling machining is very complex,” Dr. Cherukuri said. “He has come up with some innovating ways to move it forward, and has succeeded in taking models from 2D to 3D. He is an excellent student, but what truly makes him a stand out is he is self-motivated and a self-starter. He is tremendous at taking initiative and exploring other possibilities to develop solutions.”
At LLNL, Ojal will be working with the Additive Manufacturing team, which is doing research to bring deterministic design and operating principles to new processes and equipment, with the intent of transitioning technologies from laboratory to production environments. Ojal will be initially focusing fulltime on the additive manufacturing work, and then will have opportunities to do additional work in areas such as computational analysis.
“Through Dr. Cherukuri and his work between LLNL and UNCC, I got the opportunity to do an internship with LLNL last summer,” Ojal said. “I wanted to get some practical experience in additional to my computation analysis work, so I joined the project. This got me involved in the additive manufacturing collaboration, and they liked my work, which led to the post-doc position. It is a great opportunity for me getting to work for a national lab.
“I would like to thank Dr. Cherukuri for his help. In critical places such as the initial connection with LLNL, he helped a lot. And on my thesis work his guidance has been very important. I would never have gotten this opportunity without him.”
Details of Ojal’s Machine Modeling Work
The research deals with the modeling of machining using a Smoothed Particle Hydrodynamics (SPH) method. Study of machining process is important for enhancing the machining output through a better understanding of the relationship between input variables (such as tool geometry, material to be machined, etc.) and the output variables (such as cutting forces, temperature rise, tool wear, etc.). The SPH method has several advantages over grid-based methods, such as better handling of large deformations and the availability of an intrinsic material separation method for chip separation and crack formation. This is because of the lack of physical connection between the particles used for discretization.
Most of the studies to date focus on 2-dimensional machining models. Very few studies focus on the 3-dimensional modeling of machining. The objective of this work is to predict the cutting forces and chip morphology during turning operation through simulations. Starting from the 2D models, 3D models are developed and then extended to include modulated tool path (MTP) machining. The simulated cutting forces and the chip profile correlate well with the experimental observations. Since these machining models use the Johnson-Cook material model as the constitutive model, an approach for the unique determination of these parameters using the inverse methods is studied. A combination of the inverse approach using the results of orthogonal machining experiments along with tensile test experiment is proposed for the unique determination of the parameters.